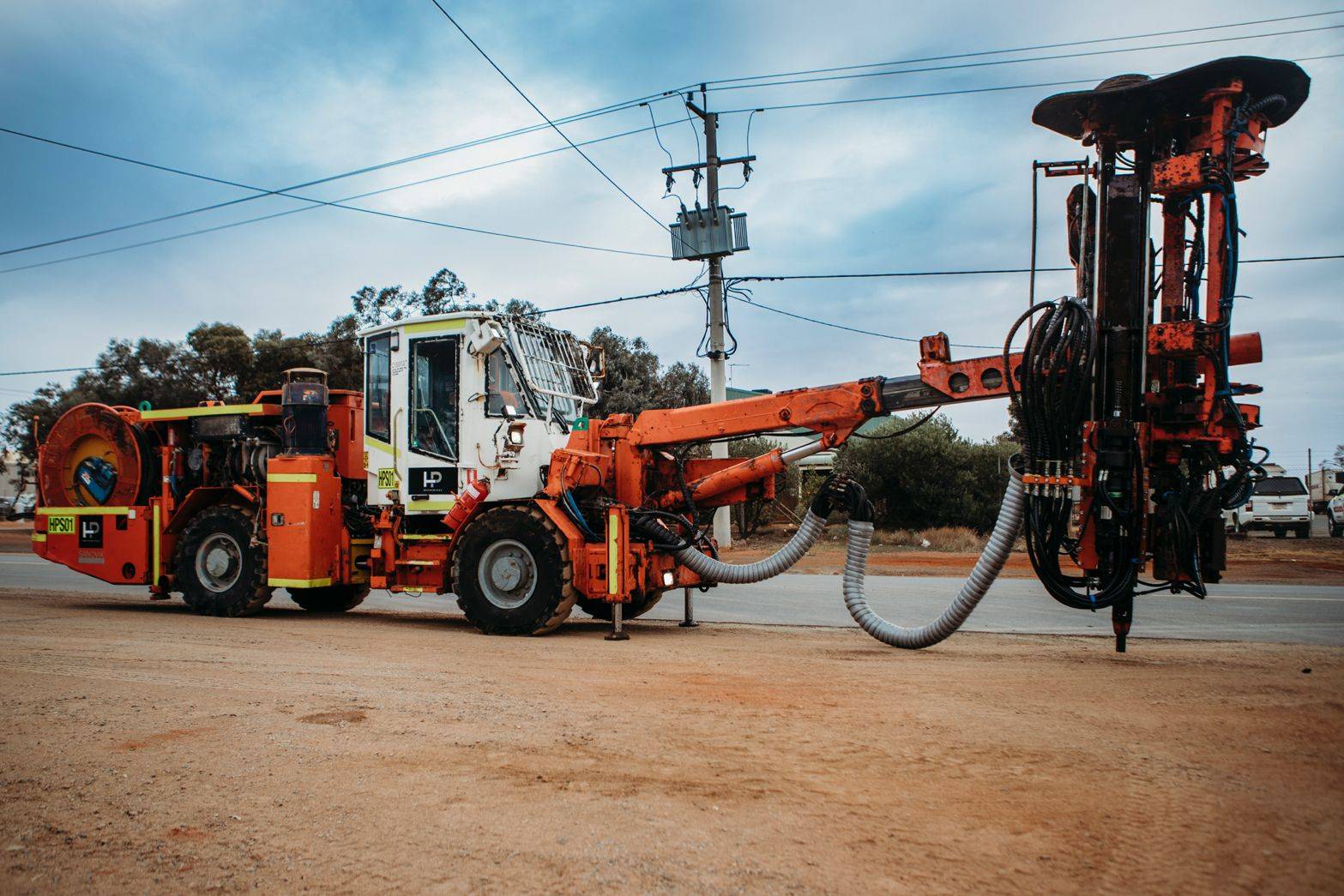
No Gap Wrap Recycling Process
The 6 Step Process
At Hydraulic Shields, we’ve designed a state-of-the-art recycling process to produce our eco-friendly No Gap Wrap product. Here’s a breakdown of our meticulous procedure:
- Shredding and Granulating: The recycling process starts by shredding large chunks of waste from both Hydraulic Shields and other partner companies. This waste is then further granulated to achieve a fine consistency.
- Erema Pelletizing: The granulated material is sent to our Erema pelletizing machine. This step involves a filtration system that removes even the tiniest of impurities. Once purified, the material is converted into pellets, which are vital for the next step in the process.
- Blend: The purified pellets are then mixed with flame retardants and colour mixtures to create the final compound.
- Compounding: The blended material is processed through a compounding extruder, followed by pelletizing. These new pellets are wet, and so they’re transported to a spin dryer which functions like a massive washing machine. After drying, the pellets are sent to a vibrator, ensuring they’re ready for final production.
- Production: The specifics of this step are a closely guarded secret, ensuring that our unique process stays exclusive to Hydraulic Shields.
- Distribution: Once produced, the No Gap Wrap is supplied to mining companies and contractors across Australia, and global partners in places like Alaska, West Africa, Saudi Arabia, and Tennessee, USA.
In the past six months, we’ve made a full transition to this comprehensive recycling system. This shift has reduced costs, allowing us to navigate through Covid/world financial changes, without the need to increase our pricing. Certainly not the trend in our industry., This also significantly benefits the environment by keeping these materials out of landfill. Our goal has always been to transition to recycled materials, and with No Gap Wrap, we’ve achieved that vision.